Application
A Gulf Coast refinery was investigating solutions during an upcoming Hydrotreater turnaround where high levels of H₂S and other sulfur compounds were anticipated to be above the regulatory levels per the new Subpart Ja requirements for total sulfur loading to flare systems. The client’s Flare Gas Recovery (FGR) unit was not available during the decontamination and deinventory phase of the turnaround and required a temporary system to remove the H₂S and Sulfur compounds from the flare line during the outage.
Vapor Point was able to design and engineer a temporary H₂S and sulfur compound removal system to meet the operational requirements of the refinery during this period. Vapor Point designed the system utilizing the VaporLock™ liquid scrubber system for high efficiency H₂S removal with engineered and ASME coded vessels, heat exchangers, monitors, emergency shutoff systems and condensate removal systems. The Vapor Point process allowed the hydrocarbon compounds to be routed to the flare system with the H₂S reduced to acceptable levels and verified by the clients CEMS monitoring system.
The expected H₂S mass was over 630 lbs over the course of the 5 day project. The project was designed around their upset conditions of 5000 cfm, which would have occurred had a sister or neighboring unit experienced unplanned releases to the flare while the Hydrotreater Turnaround was ongoing. The project parameters for basis of design was the following stages during the decontamination and deinventory of the Hydro Treater Unit.
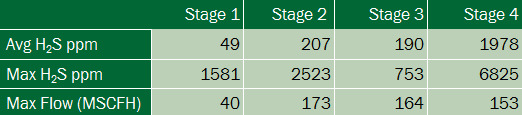
Solution
The final project design included heat exchangers to reduce the heat and potential steam condensate carry over to the vapor control system off of the primary flare line. Temporary blowers setup in parallel for back up service were put into place to capture the sulfur contaminated flare vapor stream and push through the VaporLock™ liquid scrubbers system. The VaporLock™ scrubbers and all other process equipment was engineered and constructed in parallel service to allow for redundancy in the event of mechanical failure during the decontamination and deinventory of the unit.
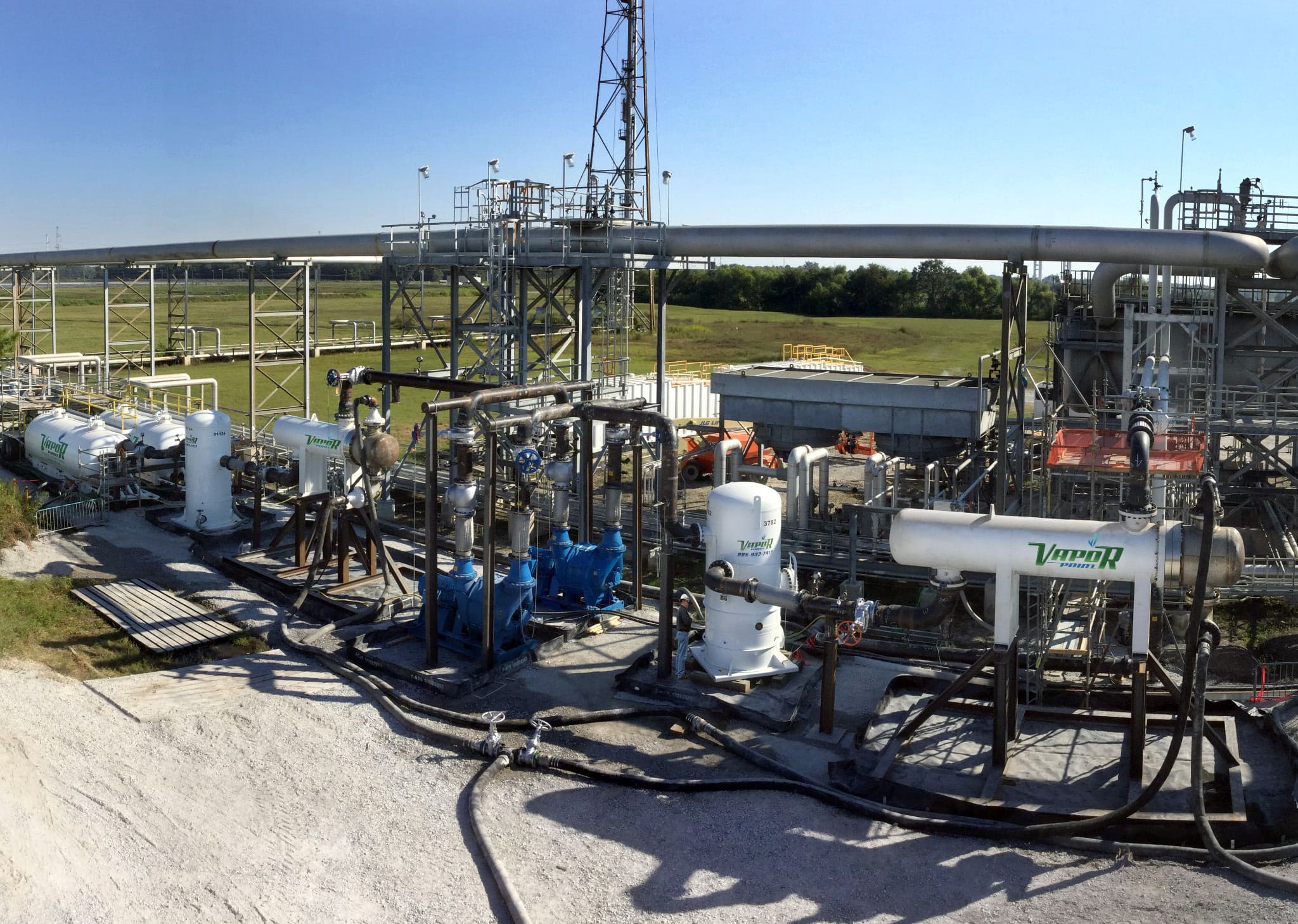
Vapor Point’s Results
The project results exceeded the clients’ expectations for meeting Ja requirements, H₂S levels as measured by the client’s CEMS were less than 76 ppm throughout the entire deinventory process, and overall flow rates of the system were maintained to allow for completion of the decontamination of the unit on schedule with no delays due to the vapor control system provided by Vapor Point. The client was highly impressed and adopted this as their best practice for managing H₂S flare gas.