Background
A West Coast Refinery was performing maintenance that required the eductors controlling their sulfur pit to be taken out of service. During this time, vapors from the pit, containing high levels of H₂S andSO₂ , would be venting to atmosphere. This would pose personnel health and safety concerns and would have been in violation of regulation 40CFR60 Subpart Ja.
Client’s Challenge
The pit itself had no pressure rating and pits typically have many leak points at ground level. H₂S and SO₂ emissions would be near ground level and pose a health and safety risk to personnel in the area and be in violation of environmental regulations. A temporary system allowed them to operate the unit under normal conditions while maintenance activities were performed.
Concerns:
- Elemental sulfur passing through the system
- Temperature of sulfur being controlled
- High levels of H₂S
- SO₂
VaporLock™ Advantages:
- Ability to operate while sump is still hot
- Helps to cool down sump and allows for earlier turnover to maintenance
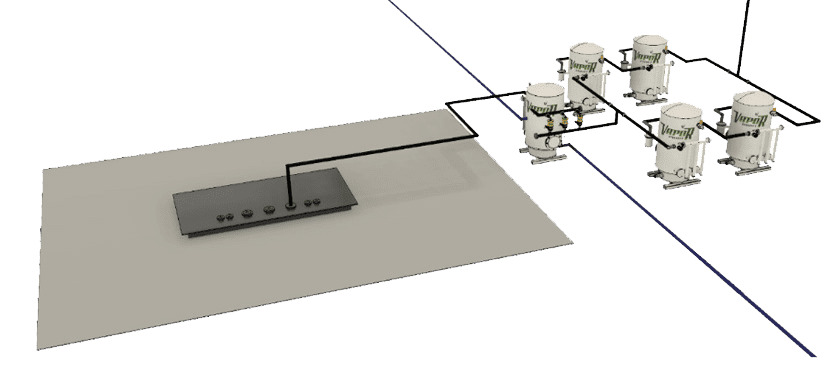
The VaporLock™ Solution
Vapor Point proposed a system consisting of a quench vessel, filled with water provided by the refinery, to lower the temperature of the vapors coming off the sulfur pit (provided temperature of 300F) and remove any solids or collapse any steam that came over. The water in the quench vessel was batched and monitored for pH and temperature to determine when the water required a change out. Stainless steel hose was used for the connection between the sump and the quench due to the anticipated elevated temperatures. Following the quench, two 48” VaporLock™ scrubbers with approximately 250 gallons of SourSorb were put in place. Based on initial estimates provided on expected maximum H₂S and SO₂ generation, the client requested two scrubbers to have sufficient chemical volume for an anticipated two day run. The vessels were plumbed to allow for each to be operated independently or for the two to be operated in series with a primary and secondary. At the outlet of the rear vessel, two air powered venturis were put in place to pull vapors from the pit and into the system. A portable CEMs unit was placed on the outlet of the system to monitor for SO₂ and H₂S being emitted to atmosphere. Outlet readings would indicate when changeouts were required for the SourSorb chemical.
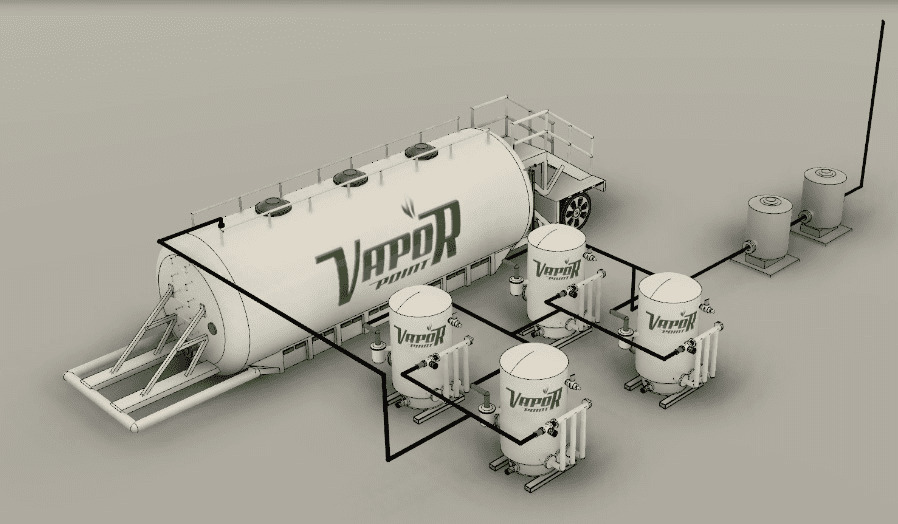
Vapor Point Results
The system operated for approximately 10 hours, during that time there was no observance of H₂S or SO₂ by the CEMS. The Vapor Point system provided a safe working environment while allowing the unit to continue normal operations remaining within the refinery’s environmental permit limitations. During operation, the CEMs unit recorded data every 10 seconds. The average SO₂ amount read on the outlet to atmosphere was 0.63 ppm. The average H₂S reading was 0.44 ppm.